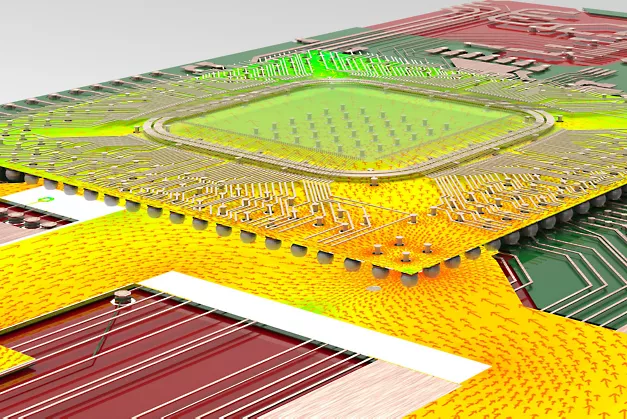
ANSYS SIGNAL INTEGRITY/POWER INTEGRITY SIMULATION SOLUTIONS
Ansys Signal Integrity (SI) and power Integrity (PI) analysis products are essential for the design of high-speed serial channels, parallel buses and complete power delivery systems found in modern high-speed electronic devices. Our integrated electromagnetics and circuit simulation products predict EMI/EMC, signal integrity and power integrity issues — enabling your design team to optimize system performance prior to build and test. Design automation features enable you to import designs from popular layout tools, perform rigorous electromagnetics extraction and then couple to full-circuit simulations. This approach enables electronics companies to achieve a competitive advantage with faster time to market, reduced costs, and improved system performance. Package and board designers use Ansys 2.5-D/3-D full-wave electromagnetic solvers along with extraction and circuit simulation tools to address signal integrity, power integrity and electromagnetic interference challenges. Engineers can use Ansys products such as Ansys HFSS and Ansys SIwave to predict Signal Integrity, Power Integrity and EMI/EMC.
Shrinking timing and noise margins are the leading contributors to signal integrity and power integrity issues in electronic products.
Ansys provides a complete suite of engineering simulation tools to help identify signal integrity and power integrity issues early in the design cycle, for electronics applications including:
- Printed circuit boards (PCBs)
- IC packages
- Connectors
- Other complex interconnects
Ansys electromagnetics and circuit simulation products predict EMI/EMC, signal integrity and power integrity issues — enabling your design team to optimize system performance prior. To build and test. Design automation features enable you to import designs from popular layout tools, perform rigorous electromagnetic extraction and then couple to full-circuit simulations.
As silicon nodes continue to shrink, so do the power rail supply voltages and noise margins. At the same time, the density of transistors increases for the same volume. Successful product operation necessitates power integrity simulation for power plane impedances. Predicting cost is essential for high-volume manufacturing and automating the process to reliably predict AC operating performance for power distribution networks significantly reduces time to market and improves performance. As silicon interposers (2.5D IC) and 3D IC designs become more prevalent, DC power loss and thermal heat mitigation become critical to product lifecycle design. Ansys provides the world’s leading simulation solution for power delivery from on-chip to package, PCB and chassis/casings. Engineers can use Ansys products such as HFSS and SIwave to predict power integrity.
For today’s high-speed digital designs, it is critical that printed circuit boards (PCB) and integrated circuit (IC) packages are accurately analyzed using a reliable simulation tool like Ansys SIwave-DC so that potential pre- and post-layout power and signal integrity problems are caught early in the design cycles. Ansys SIwave-DC provides proper verification of power delivery networks for DC power losses, early detection of thermal hotspots, and prevention of failure during the design cycle. Translation from all third party ECAD vendors can be done using SIwave-DC. Multiple layout topologies are supported: PoP, SoC, SiP, and PKG on PCB. With SIwave-DC you can:
- Avoid DC current crowding in planes, traces and vias which can lead to PCB failures and bad circuit performance
- Couple bi-directionally to Ansys Icepak to account for thermal losses (joule heating)
- Decrease warranty costs associated with thermal-cycling issues
- Debug existing PCB designs to make minor layout changes that result in major performance and reliability improvements
- Reduce trouble-shooting time in the lab and get to market faster, with a better product
Electromagnetic compatibility (EMC) and electromagnetic interference (EMI) tests are often performed very late in the product development cycle, using a fabricated PCB. This approach adds expense and leads to lengthy product development cycles when violations are discovered in anechoic chamber tests. Signal integrity and power integrity simulations can identify superfluous radiation within packages, PCBs and connectors. Such analysis can provide insight that leads to successful regulation compliance testing and provide engineers with electromagnetic field patterns and plane resonances — enabling solutions to existing signal integrity or power integrity problems within designs. Ansys Electromagnetics and circuit simulation products such as HFSS and SIwave predict EMI/EMC.
What is a Full System EMI/EMC Methodology:
- utilizing the best in class tools
- incorporating physical board layouts
- using real world transient signals
- taking into account full 3D enclosures
- seamlessly combining frequency and time domain simulation tools to predict EMI